[SatNews] Extremely complex parts can be printed and made as light as possible, but there’s a catch:
3D-printed parts promise a revolution in the space industry, rapidly creating almost any object needed. But do the results really have the right stuff for flying in space? ESA is now checking if their surface finish comes up to scratch.
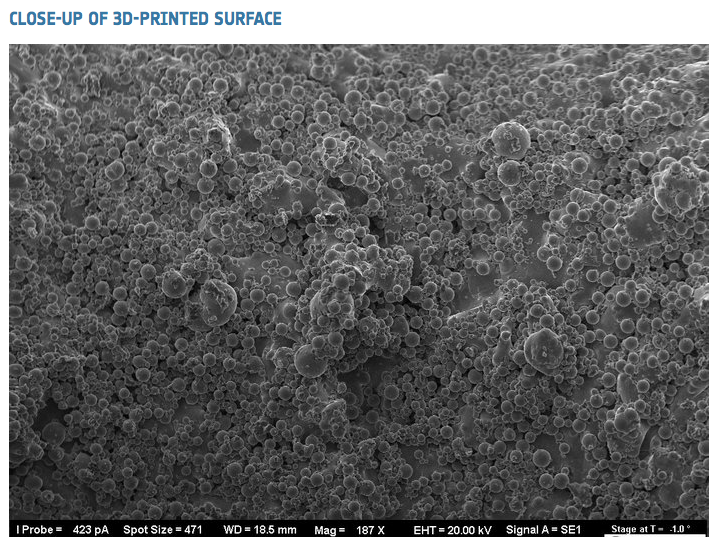
Copyright ESA Description Scanning electron microscope close-up of the surface of a part produced by Additive Manufacturing, otherwise known as 3D-printing. As a consequence of its manufacture, loose particles adhere to the solid surface, which could be troubling for use in space. The largest particles seen measure about 100 micrometers across, around the width of an average human hair.
3D printing involves building an item by laying down successive layers of material, rather than cutting away from a solid block.
ESA’s Clean Space initiative continues to look at ways of reducing the environmental impacts of space technologies—and 3D printing slashes waste.
Extremely complex parts can be printed and made as light as possible, but there’s a catch: 3D printing tends to end up with rougher surfaces than their traditional counterparts.
While this is not a major issue for terrestrial applications, there could be important consequences for their use in space. As Nobel-winning chemist Linus Pauli once observed: “‘God made solids but the devil made surfaces.”
Traditionally, materials used in space have to be as smoothly finished as possible, with no loose particles or pores that might develop cracks. They have to be clean, to surgical standards. Delicate satellite electronics or optics have in the past been fatally damaged by particle contamination or outgassing.
A new ESA project will investigate the surface features of 3D-printed parts to scrutinize the suitability of standard surface treatments for typical satellite materials such as aluminum, titanium and stainless steel.
Different manufacturing techniques, including laser and electron beam melting, will be assessed, along with surface treatments such as sandblasting, etching, nickel coating and painting.
The mechanical properties of the processed parts will be assessed for resistance to stress corrosion and the tendency to fracture.
The usefulness of ‘non-destructive’ investigations such as ultrasound and X-ray examinations will be evaluated as methods for ensuring the soundness of the parts.
These samples will also be tested against the high humidity found at ESA’s equatorial launch site in South America, as well as against the temperature extremes found in space.
Companies can tender for the project through ESA's tendering system.