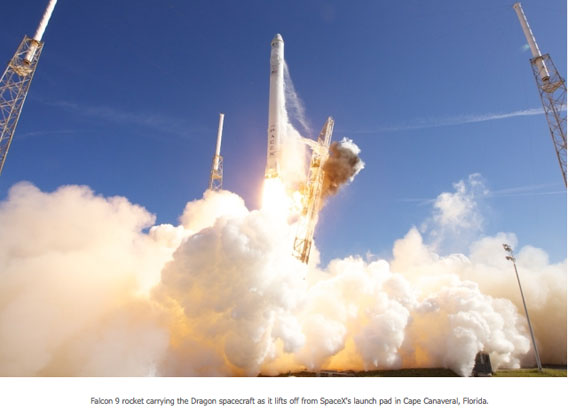
[SatNews] With a vacuum specific impulse of 311s, this is the highest performance gas generator cycle kerosene engine ever built, exceeding the Boeing Delta II main engine, the Lockheed Atlas II main engine and the Saturn V F-1.
On Monday, February 25, 2013 at 1:30 PM ET, SpaceX conducted a successful static fire test of the Falcon 9 rocket, in advance of a targeted March mission to the International Space Station.
The nine-engine test took place at the company's Space Launch Complex 40 at the Cape Canaveral Air Force Station as part of a full launch dress rehearsal leading up to SpaceX CRS-2, the second official cargo resupply mission under NASA's Commercial Resupply Services (CRS) contract.
During the static fire test, SpaceX engineers ran through all countdown processes as though it were launch day. All nine engines fired at full power for two seconds, while the Falcon 9 was held down to the pad. SpaceX will now conduct a thorough review of all data and continue preparations for Friday's targeted launch.
The first launch opportunity for CRS-2 is currently scheduled for 10:10 AM ET on Friday, March 1.
The Falcon 9 tank walls and domes are made from aluminum lithium alloy. SpaceX uses an all friction stir welded tank, the highest strength and most reliable welding technique available. Like Falcon 1, the interstage, which connects the upper and lower stage for Falcon 9, is a carbon fiber aluminum core composite structure. The separation system is a larger version of the pneumatic pushers used on Falcon 1.
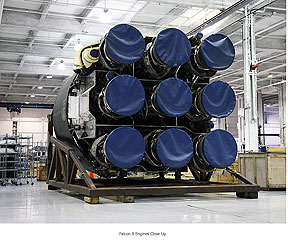
Nine SpaceX Merlin engines power the Falcon 9 first stage with 147,000 lbs-f sea level thrust per engine for a total thrust on liftoff of just over 1.3 Million lbs-f. After engine start, Falcon is held down until all vehicle systems are verified to be functioning normally before release for liftoff.
The second stage tank of Falcon 9 is simply a shorter version of the first stage tank and uses most of the same tooling, material and manufacturing techniques. This results in significant cost savings in vehicle production.
A single Merlin engine powers the Falcon 9 upper stage with an expansion ratio of 117:1 and a nominal burn time of 345 seconds. For added reliability of restart, the engine has dual redundant pyrophoric igniters (TEA-TEB).
The main engine, called Merlin, was developed internally at SpaceX, but draws upon a long heritage of space proven engines. The pintle style injector at the heart of Merlin was first used in the Apollo Moon program for the lunar module landing engine, one of the most critical phases of the mission.
Propellant is fed via a single shaft, dual impeller turbo-pump operating on a gas generator cycle. The turbo-pump also provides the high pressure kerosene for the hydraulic actuators, which then recycles into the low pressure inlet. This eliminates the need for a separate hydraulic power system and means that thrust vector control failure by running out of hydraulic fluid is not possible. A third use of the turbo-pump is to provide roll control by actuating the turbine exhaust nozzle (on the second stage engine).
Combining the above three functions into one device that we know is functioning before the vehicle is allowed to lift off means a significant improvement in system level reliability.
Sea Level Thrust : 147,000 lbf
Vacuum Thrust: 161,000 lbf
Sea Level Isp: 282s
Vacuum Isp: 311s
With a vacuum specific impulse of 311s, Merlin is the highest performance gas generator cycle kerosene engine ever built, exceeding the Boeing Delta II main engine, the Lockheed Atlas II main engine and the Saturn V F-1.