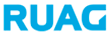
[SatNews] Swiss company RUAG Space plans to soon be equipping satellites with components made using a 3D printer—making them lighter and cheaper.
As part of a pilot project, specialists at RUAG Space have built an antenna support for an Earth observation (EO) satellite. RUAG previously supplied the European Space Agency (ESA) with a similar support for its Sentinel-1A radar satellite, although the support for ESA was manufactured using conventional methods. Collaborating with experts from the company Altair, RUAG engineers have now completely redesigned this support to optimize it for 3D printing. The Altair Software made it possible to exploit the freedom of design provided by additive manufacturing by optimizing the topology of the component in order to use only as much material as necessary. Produced by EOS (EOS e-Manufacturing Solutions), a German specialist for industrial 3D printing, the finished component is just half as heavy as the previous component and has better rigidity. Some 40 cm long, the antenna support is one of the largest components ever produced using the powder-bed manufacturing method.
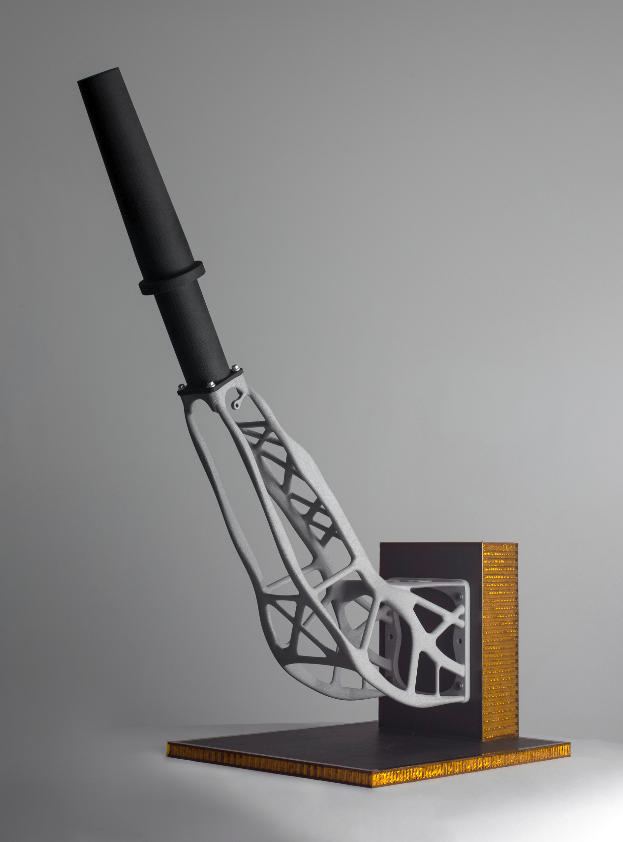
3D printed Antenna Bracket for a Sentinel-1-Satellite
To check that the new support is ready for use in space, it is currently undergoing a battery of intensive qualification tests that are scheduled to be completed by the end of the year.
“Our goal is to fit Sentinel-1 successors with antenna supports that have been manufactured using a 3D printer,” said RUAG Space CTO Michael Pavloff.
RUAG Space has been conducting intensive research and development work on how to “print” objects in three dimensions—a process known as Additive Manufacturing—since 2013. Making a 3D print involves building up layers of powder and joining them together to form the desired shape in an automated process of direct metal laser melting.
Compared to conventional processes, Additive Manufacturing offers a host of benefits – producing metal and plastic components that are lighter, take less time to manufacture and are ultimately cheaper to produce. Weight reduction is a decisive factor in the space industry, since the lighter a satellite is, the less it costs to send it into space.
Producing this antenna support is by no means a one-off.
“3D printing has enormous potential for our business, and we’re currently in the process of developing further space applications,” said Pavloff.
In the future it will also be possible to create entire satellite structures using a 3D printer. This means that electrical harnesses, reflectors, heating pipes and other assemblies that today still have to be manufactured individually could then be integrated directly into the structural elements.
The design specialists at Altair also benefit from the joint project.
“The collaboration with RUAG Space and EOS allows us to deliver even more innovative end-to-end design and optimization processes to exploit the benefits of additive manufacturing.” said Altair Managing Director Pietro Cervellera.
For more information, please visit the RUAG Space infosite